1.Präambel
Einteilige Türringe erfreuen sich aufgrund ihrer Wirtschaftlichkeit und Sicherheit bei großen Automobilherstellern großer Beliebtheit.Aufgrund der unterschiedlichen Kraft- und Strukturanforderungen verschiedener Teile müssen unterschiedliche Dicken in verschiedenen Teilen, sogenannten Verstärkungsblechen oder Patchplatten, realisiert werden. Daher müssen diese nach dem maßgeschneiderten Schweißen des Türklopfers und vor dem Thermoformen vor dem Punktschweißen hergestellt werden wird mit der Patchplatte benötigt (wird hauptsächlich für die AB-Säulenverstärkungsplatte verwendet).
Prozessanalyse:
2. Das Grundmaterial des einteiligen Türrings vor dem Thermoformen besteht hauptsächlich aus Borstahl, die Streckgrenze beträgt 280–400 MPa und die Schweißleistung ist gut.In Anbetracht der Tatsache, dass die Form des Türringmaterials größer ist als nach dem Formen und es viele Lötstellen auf dem Patchboard gibt, wird häufig die automatische Zuführmethode und das automatische Punktschweißen nach der Montage verwendet.
3. Fall:
Der Türklopfer eines M-Projekts einer Automobilfabrik, Material 22MnB5, Dicke 1,6 mm, zwei Patchplatinen, insgesamt 78 Lötstellen, wurde uns durch die Einführung eines Freundes gefunden, wir verwenden automatisches Laden von Robotern, Punktschweißen von Roboterschweißbrennern und automatisches Entladen.
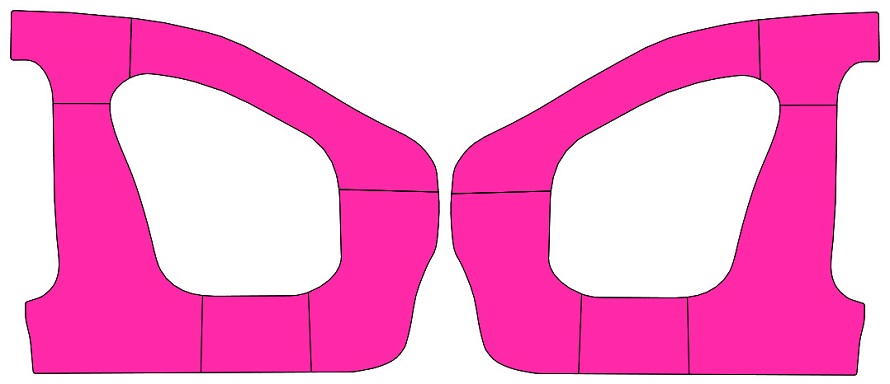
3.1 Schema-Layout:
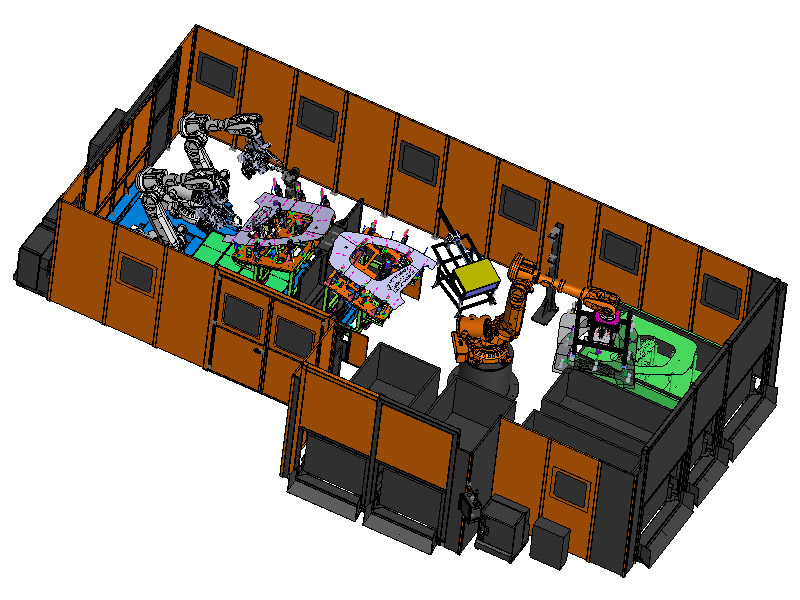
3.2 Projekteinführung
Das ankommende Material liegt in Form eines Materialwagens vor, der im Wesentlichen die Form des Werkstücks vorgibt, es dann durch den Saugnapf des Roboters ergreift, die Position kalibriert und es zum Drehtischwerkzeug transportiert, und nach dem Spannen wird es dann bearbeitet Markiert durch zwei Anjia-Schweißbrenner (aufgrund der großen Anzahl von Lötstellen werden zum Punktschweißen Doppelpistolen verwendet). Nach dem Punktschweißen entlädt der Roboter das Material auf den Zuführwagen.
a.Greifstation: Das Werkstück wird vom Vakuumsauger vom Materialwagen angesaugt und nach Erreichen des Drehtellers an das Werkzeug übergeben.
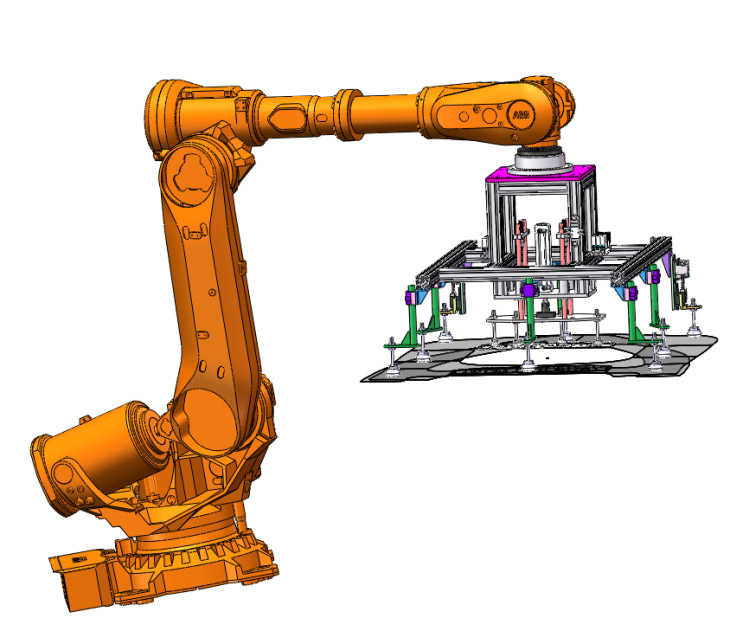
B.Doppelschweißzangenstation: Zwei Roboterschweißzangen werden simuliert und synchron nach der besten Bahn geschweißt;
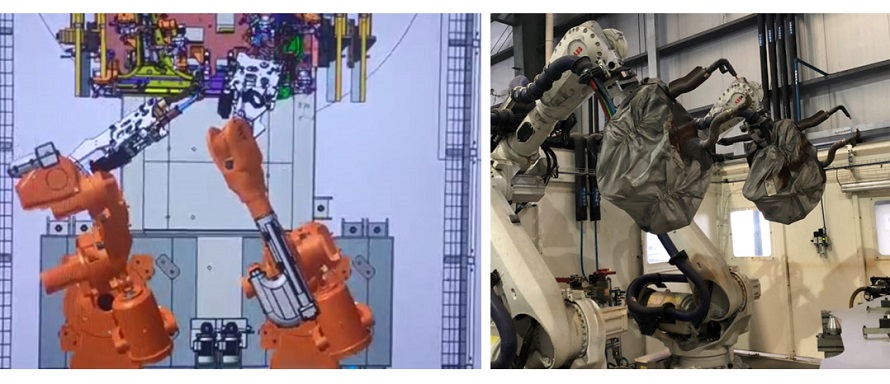
B.Rotierende Werkzeuge: Aufgrund der großen Form des Werkstücks werden geneigte Werkzeuge verwendet, um den Platzbedarf zu verringern und den erreichbaren Hub des Roboters zu verkürzen.
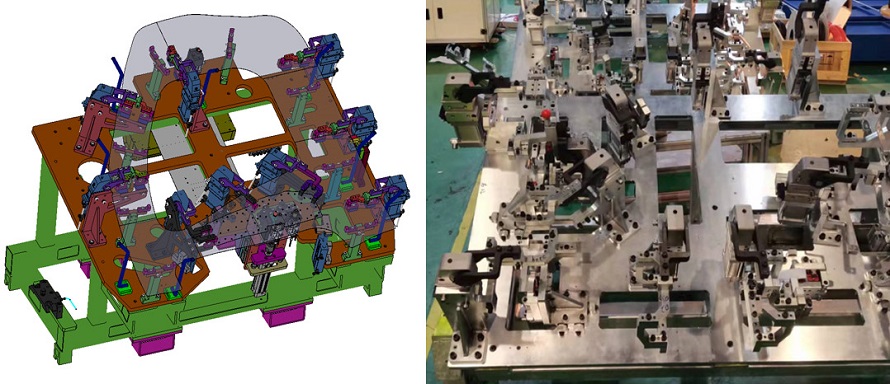
b.Inspektion und Überprüfung: Der Durchmesser der Schweißlinse bei der Nachschweißprüfung überschreitet Ø6 und der Schweißzyklus wird innerhalb der Anforderungen kontrolliert.
C.Abschluss:
Das Materialpunktschweißen von integral geformten Türklopfern ist aufgrund des flachen Materials und der vielen Schweißpunkte relativ einfach zu realisieren, was deutlich weniger schwierig ist als das automatische Punktschweißen nach der Umformung, und auch das angewandte Punktschweißverfahren ist relativ traditionell.Der einzige Unterschied besteht darin, dass die Form des Produkts größer ist, was bestimmte Anforderungen an das Gesamtlayout des Arbeitsplatzes stellt;In Zukunft werden immer mehr Türklopferanwendungen integriert, und die Verwendung von automatischen Punktschweißblechen vom Portaltyp wird ebenfalls eine gute Wahl sein.
Schlagwort: Einführung des Schweißprozesses für automatische Punktschweißarbeitsplätze für Bleche von Autotürknöpfen – Suzhou Agera Automation Equipment Co., Ltd.
Beschreibung: Der vollautomatische Punktschweißarbeitsplatz für Autotürklopfer basiert auf Faktoren wie flachen Materialien, vielen Lötstellen und großen und schweren Türklopfern.Schweißen.
Schlüsselwörter: Automatischer Punktschweißplatz für Autotürring-Rohling, Roboterschweißsystem für Autotürring-Rohling, Schweißprozess
Zeitpunkt der Veröffentlichung: 16. Februar 2023