板金溶接は多くの産業で使用されています。金属部品を接合する必要があるときは、溶接方法を検討します。溶接技術は非常に進歩しており、適切な溶接方法を選択することで作業がはるかに簡単かつ効率的になります。この記事では、板金溶接について理解し、適切な溶接方法を見つけるのに役立ちます。
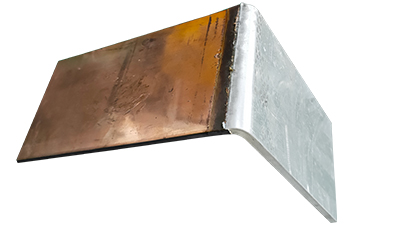
板金溶接とは何ですか?
シートmエタール溶接材料加工技術であり、二あるいは複数の金属部品を何らかの方法で一つに分離する。産業技術の発展に伴い、溶接技術はますます広く使用されており、製造業の金属加工における重要なプロセスです。
金属の溶接にはどのような方法があるのでしょうか?
金属の溶接方法には多くの種類があり、溶接工程における金属の状態や加工特性に応じて、主に溶融溶接、圧接、ろう付けの3つに分類されます。
溶融溶接
溶融溶接は、金属部品を加熱して溶かして接合する方法です。この方法は圧力を必要としません。 2 つのワークピースの界面が加熱されると、金属に大きな原子間力が発生し、加熱された領域に液体状態が形成されます。 2 つのワークピースの金属原子は完全に拡散し、融合します。溶けた金属が冷えると、強力な溶接接合部が形成されます。
一般的な溶融溶接技術には、アーク溶接、ガス溶接、レーザー溶接などがあります。
アーク溶接
アーク溶接電源によって電力が供給され、電極と 2 つのワークピースの間で放電してアークを形成します。このアークは熱に変換され、電極とワークピースを溶かし、金属を接合します。溶接プロセス中、低電圧と高電流により高温と強い光が発生し、電極とワークピースが燃焼して溶融池が形成され、冷却されて溶接部が形成されます。
この溶接方法は応用範囲が広く、ステンレス鋼、アルミニウム、銅、高炭素鋼などのさまざまな金属の溶接に使用できます。アーク溶接装置は持ち運びが容易で操作が簡単なため、機械製造、建設、造船などの業界で広く使用されています。たとえば、建設における鉄筋の接続に使用されます。さらに、アーク溶接は機器の修理や線路の保守にも頻繁に使用されます。
アーク溶接には通常、アーク溶接機、溶接棒、フェイスシールドが必要です。低コストで広く使用されている溶接方法です。ただし、技術的に難しいため、溶接の品質は溶接者のスキルレベルに大きく依存します。
ガス溶接
ガス溶接燃料ガスと酸化ガスの2種類のガスを使用します。このガスの燃焼により熱が発生し、この熱で金属材料と溶接棒が溶融し、2つのワーク間に連続的に供給され、金属接合が完了します。
ガス溶接は、鋼、アルミニウム、銅などの金属の溶接によく使用されます。適用の柔軟性、作業環境の制限がない、操作が簡単などの利点があります。また、電気を必要としないため、屋外作業や工事現場の金属接続などに広く使用されています。金属パイプを修理する必要がある場合、ガス溶接は優れた選択肢です。
ただし、ガス溶接には限界があります。溶接の品質は溶接棒の品質に大きく影響され、溶接継手は変形しやすくなります。また、生産効率も比較的低い。
レーザー溶接
レーザー溶接熱源としてレーザー光線を使用します。レーザー ビームが金属ワークの端に当たると熱が発生し、溶融池が形成されます。レーザーが遠ざかると、溶融金属のエッジが冷えて結合します。この方法は、さまざまな産業用途でオーバーラップ溶接、突合せ溶接、およびシール溶接に使用できます。
レーザー溶接は溶接速度が速く、効率が高く、非金属の溶接にも使用できます。自動車製造、エレクトロニクス、宝飾品などの業界で広く使用されている高度な溶接技術です。ただし、厚い材料には浸透できないため、薄肉材料に最適です。他の溶接方法と比較すると、レーザー溶接装置は高価になる傾向があります。
プレス溶接
融接とは異なり、圧接では溶接プロセス中に金属に一定量の圧力を加える必要があります。金属材料は溶けて液体にならず、固体のままです。加圧溶接では、金属接合部を加熱して可塑性を高め、その後、可塑化した金属に圧力を加えて、より強力な溶接接合部を形成します。したがって、圧力はプロセスにおいて重要な役割を果たします。
産業経済の発展に伴い、多くの新素材や新製品が登場し、圧接技術は継続的に革新されています。現在の主な圧接技術には、抵抗溶接、拡散溶接、摩擦溶接、超音波溶接などがあります。
抵抗溶接
抵抗溶接電流を使用して金属ワークピースの接続点を加熱しながら、電極を通して圧力を加えて溶接を完了します。ステンレス鋼、銅、アルミニウム、炭素鋼の溶接によく使用されます。抵抗溶接はその高く安定した溶接品質により、自動車、エレクトロニクス、航空宇宙産業で重要な役割を果たしています。技術の進歩に伴い、抵抗溶接では自動化が進んでおり、生産効率がさらに向上しています。
抵抗溶接は次の 4 つの方法に分類できます。スポット溶接、プロジェクション溶接、シーム溶接、 そして突合せ溶接。たとえば、金属板にナットを取り付けるなど、自動車部品を溶接する必要がある場合、プロジェクション溶接を使用できます。しかし、抵抗溶接装置は一般に大きく、移動が難しいため、特定の設定での使用が制限されます。異なる金属材料や厚さを溶接するたびにパラメータを調整する必要があるため、金属部品の大量溶接により適しています。
拡散溶接
拡散溶接拡散接合とも呼ばれるこの方法では、溶接中に金属表面を加熱し、圧力を加えます。このプロセスにより、高温高圧下で金属材料の原子と分子が拡散し、結合します。拡散溶接は、類似した材料と異なる材料の両方に使用でき、一般に銅、アルミニウム、複合材料を接続します。
この方法では、20 層の 0.1 mm 銅箔を溶接するなど、アセンブリ内の複数の接合部を同時に溶接できます。拡散溶接により、変形に強い強力な接合が作成されるため、通常はさらなる加工が不要になります。しかし、生産効率が低く、設備コストが高いなどの欠点もあります。
摩擦圧接
摩擦圧接圧力下でのワークピース間の相対摩擦運動から発生する熱を利用する溶接プロセスです。これは、高品質の溶接を実現する効率的で省エネな方法です。フラッシュバット溶接と比較して、摩擦溶接は熱影響部が小さく、異種金属の接合に適しています。
摩擦圧接は独特で、低消費電力や環境に優しいなどの利点があり、機械製造、航空宇宙、エネルギーなどの業界で普及しています。ただし、一般に、同じ直径の金属棒とパイプを接続する場合にのみ適しています。ワークの形状や組み付け位置が決まると、溶接は難しくなります。
超音波溶着
超音波溶着では、超音波によって発生する高周波振動を利用して、金属接触面に摩擦、変形、熱を生じさせます。上下のサウンドホーンによって圧力が加えられ、溶接プロセスが完了します。ワークに電流を流したり、外部熱源を使わないユニークな溶接方法で、摩擦溶接や拡散溶接と共通する特徴があります。
超音波溶着銅、アルミニウム、金、銀などの同種金属と異種金属の両方を含む、さまざまな材料に使用できます。ただし、ABS、PP、PC などの非金属材料の溶接によく使用され、さらに優れた結果が得られます。
ろう付け溶接
ろう付けワークの融点より低い溶加材を加熱して溶かし、2つの金属ワーク間の隙間を埋めて金属接合を完了する溶接方法です。融着や圧接とは異なり、ワークを溶かしたり、圧力を加えたりする必要がありません。ろう付けは主に重なり合ったワークピースを接合するために使用され、ギャップ サイズは通常 0.01 ~ 0.1 ミリメートルの範囲です。
今日、ろう付けは、機械、電子機器、機器、照明などの業界全体でますます使用されています。ろう付けの品質は、使用する溶加材に大きく依存します。したがって、金属ワークをろう付けする場合は、接合部を効果的に充填できる、濡れ性の良い溶加材を選択することが重要です。ろう付けは、溶加材の融点により軟ろう付けと硬ろう付けに分類されます。
ソフトはんだ付け
ソフトはんだ付けでは、融点が 450 ℃ 未満の金属溶加材を使用します。半田付けによる接合部は強度が低く、耐熱性も劣ります。精密電子製品の電気接続やはんだごてによるはんだ付けによく使用されます。強度要件が重要ではなく、金属フィラーの融点がはんだ付けされる金属の融点よりも高い場合は、ソフトはんだ付けを使用できます。
ハードソーlデリング
硬はんだとして知られる高融点金属フィラーによるろう付けでは、摂氏 450 度を超える融点を持つ金属フィラーが使用されます。固いはんだ付けによって作成された接合は、柔らかいはんだ付けによる接合に比べて強度が高くなります。硬はんだ付けでは、一般的に銀、アルミニウム、銅、ニッケルなどの材料が使用されます。溶加材の選択は、ワークピースの材料の特性と接合部の性能要件によって異なります。硬はんだ付けは、一般に、ステンレス鋼、アルミニウム合金、銅、および高強度が要求されるその他の材料に適しています。高温下で動作するジョイントに使用され、航空宇宙、エレクトロニクス、電気産業で広範囲に応用されています。
結論
金属溶接にはさまざまな種類があり、上記の溶接は最も一般的な方法の 1 つです。溶接技術の進歩に伴い、より多くの溶接方法が登場しています。金属ワークの溶接方法を考える際には、ワークの材質、形状、作業環境などを考慮することが重要です。これらの要素に基づいて適切な溶接方法を選択することが重要です。
投稿日時: 2024 年 6 月 19 日